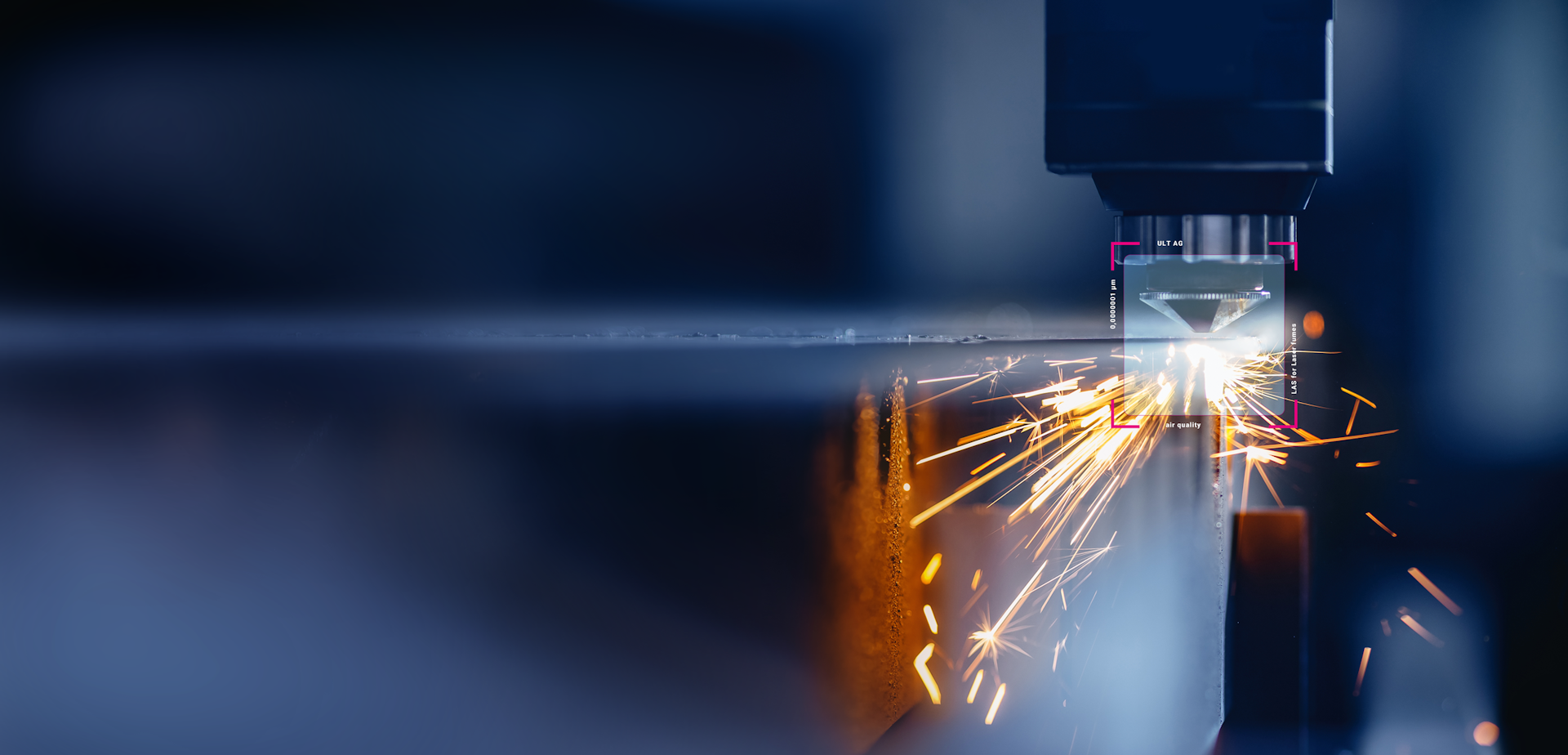
Absauganlagen für Laserrauch und Laserstaub
Ihre Top-Lösung zur Laserrauchabsaugung: LAS 260.1
Die Absaugungsanlage LAS 260.1 ist eine flexible Lösung, die für viele Laserbearbeitungsprozesse unterschiedlichster Materialien eingesetzt werden kann.
Egal ob Metall, Kunststoff oder Holz, LAS 260.1 sorgt für eine zuverlässige Absaugung und Filtration von Partikeln und Gasen aus Ihrem Prozess. So können Sie sicher sein, dass Ihre Arbeitsumgebung und Anlagen stets sauber und sicher bleiben und Ihre Produktion leistungsfähig und stabil ist.
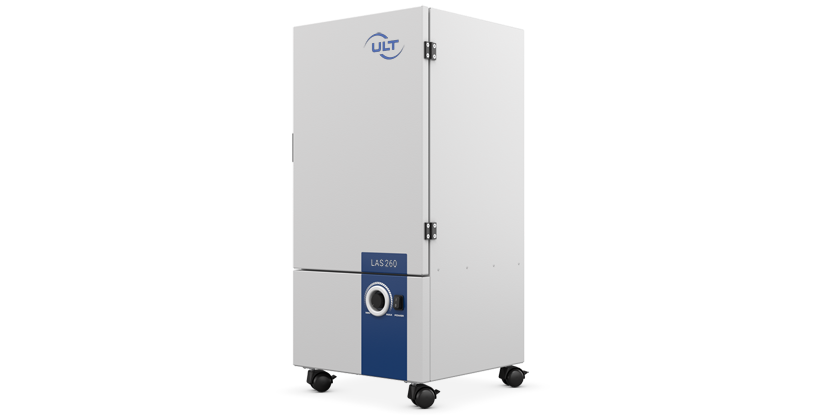
Laserrauchabsaugung bei der Materialbearbeitung
Lasermarkieren, Laserschneiden, Laserschweißen, Laserauftragschweißen, Laserstrukturieren, Laserablation oder der Einsatz von Lasertechnik in der Additiven Fertigung sind Ihnen bekannte Prozesstechnologien? Sie arbeiten mit Lasersystemen und sind auf der Suche nach einer Absauganlage, die Ihre anwendungsspezifischen Anforderungen erfüllt?
Die Geräteserie LAS deckt den gesamten Bedarf an Absauganlagen und Filtertechnologie für Laserrauch und Laserstaub ab – für alle Branchen und alle möglichen Applikationen - auch und besonders die schwierigen.
Geräteübersicht Speicherfilteranlagen für Laserrauch
Geräteübersicht Patronenfilteranlagen für Laserrauch
Die flexible Lösung zur mobilen Laserrauchabsaugung
Unsere auf mobilen Einsatz optimierte Gerätevariante mit ansprechender Formensprache ist der JUMBO Filtertrolley LAS. Die mobile Absauganlage für Laserrauch und -staub kann flexibel unterschiedlichsten Arbeitsplatz- und Emissionsbedingungen angepasst werden.
Dabei agiert die Anlage flüsterleise und dennoch leistungsstark.
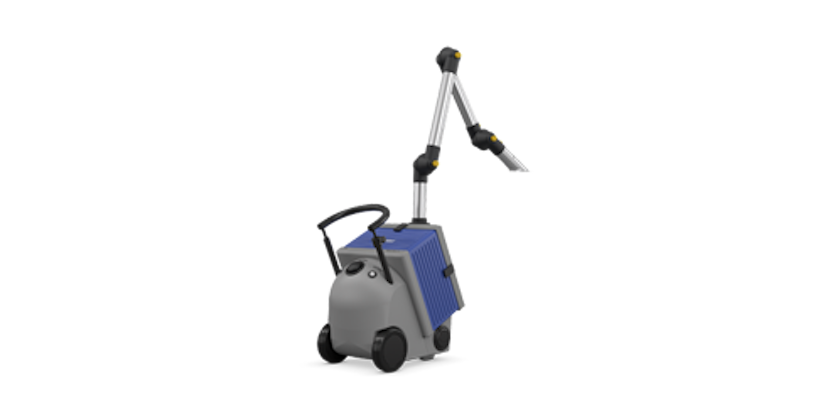
Informationen zur Laserrauchabsaugung
Webcasts on demand
Herausforderungen bei der Laserrauchabsaugung
Absaug- und Filtertechnik für Laserprozesse
Empfehlungen Absauganlagen für Lasersysteme von Keyence und Universal
Gefahrstoff-Träger Laserrauch
Laser kommen zunehmend bei der Bearbeitung von Metallen oder Kunststoffen zum Einsatz, unter anderem beim Laserschweißen, Laserschneiden, Lasergravieren, Lasersintern etc. − und auch in der additiven/generativen Fertigung.
Bei der Metallbearbeitung etwa entstehen Stäube, die beispielsweise Schwermetalle enthalten können, welche sich im menschlichen Körper anreichern können. Bei der Bearbeitung legierter Metalle werden die enthaltenen Teilsubstanzen frei, etwa Nickel, Chrom oder Kobalt. Organische Materialien werden pyrolysiert, wodurch ebenfalls hochgiftige Substanzen wie Dioxine oder Chlorwasserstoff entstehen können. Laserrauch beinhaltet zudem Feinstaub, der im schlimmsten Fall zu Atemwegserkrankungen, Herz-Kreislauf-Problemen und zu einem erhöhten Krebsrisiko führen kann.
Von der Arbeitsqualität durch permanente Rauch- und Geruchsbelästigung abgesehen, können aber auch Maschinen durch Verschmutzungen und chemische Reaktionen ihrer Produkte geschädigt werden. Gerade im Bereich feinmechanischer Arbeiten, bei denen die Präzision längst im Mikrometer-Bereich angekommen ist, ist jede Art von Beeinflussung durch Partikel zu vermeiden.
Auswirkungen haben entstehende Luftschadstoffe jedweder Größe stets auf Menschen, Maschinen und Produkte. Mitarbeiter, die langfristig wegen Krankheit ausfallen, haben neben dem Gesundheitsaspekt ebenso ökonomischem Einfluss auf ein Unternehmen wie Maschinen, die aufgrund von Verschmutzungen nicht präzise fertigen. Wartungsarbeiten, Nachproduktionen und folglich Imageverlust, sowie schwindende Kundenanfragen sind nur einige negative Auswirkungen.
Absaugen und Filtern von Laserrauch oder Laserstaub geht weit über das Industriesauger-Prinzip hinaus. Denn es gilt nicht nur, Schmutz zu beseitigen, sondern vor allem Gefahrstoffe aus der Luft zu entfernen, die weitaus mehr als eine Stauballergie auslösen können.
Die LAS-Serie an Absauganlagen und Filtertechnik von ULT sorgen für saubere Arbeitsbedingungen. Versprochen!
Ihr Kontakt zu uns
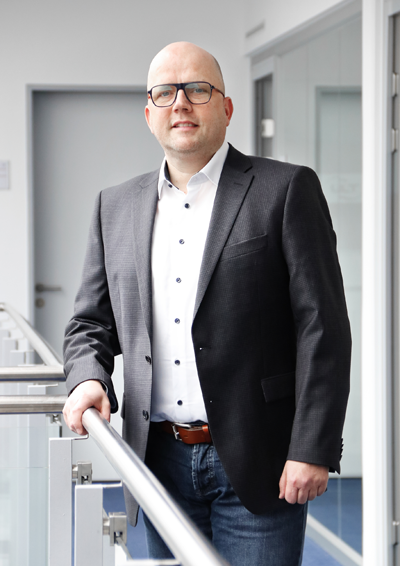
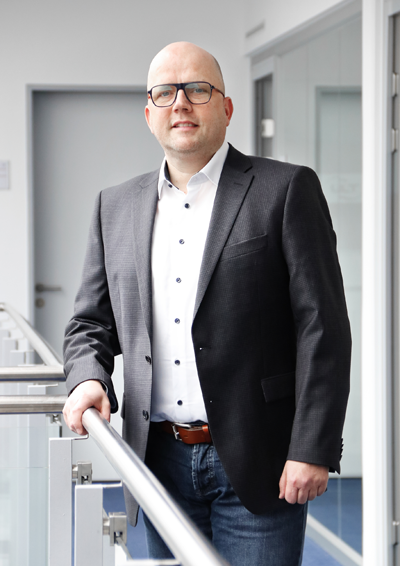